BLOG 4 MINUTE READ
iGEMBA:
Transforming Gemba Walks for Operational Excellence in the Digital Era
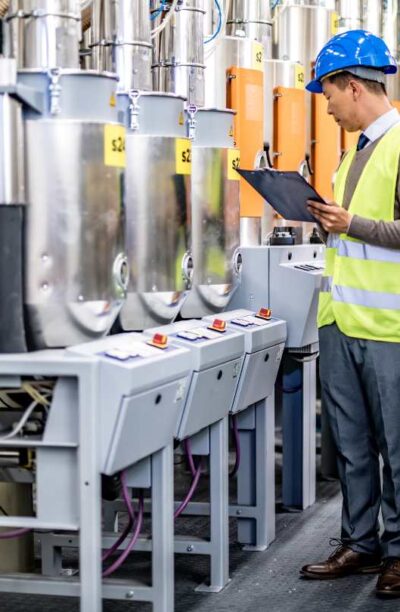
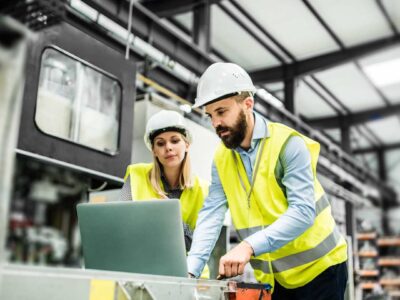
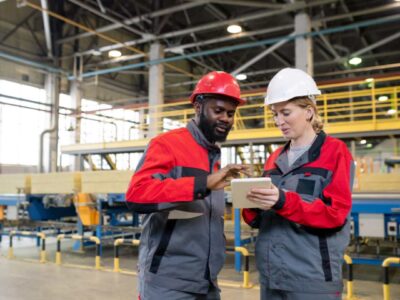
Understanding
GEMBA walk
Challenges of
traditional GEMBA
Introducing
iGEMBA
Start your iGEMBA
FREE TRIAL
Understanding
GEMBA walk
Challenges of
traditional GEMBA
Introducing
iGEMBA
Start your iGEMBA
FREE TRIAL
Unveiling the Power of Gemba Walks in the Manufacturing Ecosystem
The Gemba walk, originating from the Japanese philosophy of continuous improvement (Kaizen), involves going to the actual workplace to observe, understand, and improve processes.
It is a hands-on approach that provides leaders with a first-hand view of daily operations, fosters real-time engagement, empowers frontline employees, and promotes a culture of continuous improvement. Gemba walks provide invaluable insights into operational workflows, identify inefficiencies, gain insights into the challenges faced by frontline employees, and cultivate a collaborative environment.
However, relying solely on human observation comes with its constraints. Traditional Gemba walks face a lack of standardized documentation, creating difficulties in monitoring changes over time, disseminating insights across the organization, and assessing the impact of improvement initiatives. Furthermore, human observations during Gemba walks are susceptible to subjectivity and can be influenced by personal biases. Inadvertently, leaders may concentrate on specific areas or issues, potentially neglecting more extensive operational challenges.
However, relying solely on human observation comes with its constraints. Traditional Gemba walks face a lack of standardized documentation, creating difficulties in monitoring changes over time, disseminating insights across the organization, and assessing the impact of improvement initiatives.
Furthermore, human observations during Gemba walks are susceptible to subjectivity and can be influenced by personal biases. Inadvertently, leaders may concentrate on specific areas or issues, potentially neglecting more extensive operational challenges.
Challenges of Traditional Gemba Walks:
From Blind Spots to Missed Opportunities
Challenges of Traditional Gemba Walks: From Blind Spots to Missed
Opportunities
- Limited Frequency and Duration: Traditional Gemba walks are often infrequent and of limited duration. Leaders may struggle to gain comprehensive insights into daily operations due to time constraints, potentially missing critical observations.
- Inconsistent Documentation: The lack of standardized documentation in traditional Gemba walks poses a challenge. Without a uniform approach to recording observations, it becomes difficult to track changes over time, hindering the ability to measure progress and share insights consistently.
- Subjectivity: Human observation, while invaluable, can be subjective and prone to biases. Different leaders may interpret the same situation differently, leading to inconsistencies in feedback and action.
- Limited Historical Context: Lack of readily available historical data makes it difficult to compare current observations with past performance, hindering analysis of progress and identification of recurring issues.
- Time-Intensive Data Analysis: The manual nature of data collection in traditional Gemba walks can make the subsequent analysis time-intensive. Leaders may struggle to process and derive meaningful insights from the collected data efficiently.
- Decrease in Operational Efficiency: Traditional methods of capturing and reporting Gemba walk findings often involve manual processes and lengthy communication chains, delaying the implementation of necessary corrective actions and hindering the organization’s operational efficiency.
- Decrease in Customer Satisfaction: Traditional Gemba walks, with their periodic and time-consuming nature, may slower response to identified issues. This delay in addressing operational challenges can translate into extended lead times and ultimately dissatisfied customers.
iGEMBA: Digitizing the Path to Operational Excellence
ITHENA’s iGEMBA solution steps in as the digital bridge between the physical Gemba and the world of data-driven decision-making. It transforms the traditional Gemba walk into a powerful tool for capturing, analyzing, and leveraging insights for continuous improvement. It strategically addresses and overcomes the challenges associated with traditional Gemba walks, leading to significant improvements in organizational efficiency.
Key features of iGEMBA include:
Single-view of Shop Floor
KPIs
Standardized
Documentation
Proactive Issue
Resolution
Trend Identification and
Pattern Recognition
In-depth Root Cause
Analysis
Historical Data at
your Fingertips
iGEMBA, therefore unlocks a multitude of benefits for its users that include:
Enhanced Product
Quality
Real-time Shop
Floor Insight
Improved Customer
Satisfaction
Efficient and Proactive
Issue Resolution
Seamless Collaboration across Teams and Departments
Real-time Visibility into Shop
Floor Operations
Supercharged Operational
Efficiency
Step into the Future with iGEMBA – Where Data Empowers Decisions and Continuous Improvement Drives Excellence
The factory floor is no longer just a physical space; it’s a dynamic ecosystem brimming with data-driven opportunities. With iGEMBA, you can unlock the transformative power of Gemba walks, turning observations into actionable insights and propelling your organization towards operational excellence. By embracing the future of Gemba, you’re not just taking a step; you’re taking a leap into a world where data empowers decisions, insights guide actions, and continuous improvement becomes the heart of your manufacturing DNA.
Ditch the paperwork and unlock insights with iGEMBA!
Click here to know more about iGEMBA.